从汽车车身进步看汽车板及深加工技术的发展
2014-10-24 11:04 来源: 我的钢铁网
在节能、环保、安全和舒适性多重因素的作用和牵引下,汽车的轻量化已成大势所趋,近年来这个势头加速发展,已形成全球化潮流。研究表明,汽车车身自重每减少10%,可以降低油耗6%-8%,降低二氧化碳排放13%。汽车车身安全减重是轻量化的重要方向之一,为此汽车行业和原材料行业都高度关注车身结构优化和车身材料升级的研究。本文从解析欧洲、日本和北美最新汽车车型车身结构出发,从车身轻量化需求的角度来观察和分析汽车板及其深加工技术的发展。
1、汽车钢板与有色金属及非金属材料的竞争
传统的汽车车身用材料以钢铁材料为主,随着铝合金、镁合金及非金属材料研究的发展,汽车车身用材料的选择呈多样化。从2012-2013年欧洲车身会议发布的车型数据分析(如表1所示),2012年(EuroCarBody 2012),8款车型中6款车身使用了95%以上的汽车钢板,2款车身(奔驰SL和陆虎揽胜)以铝合金材料为主,有1款使用了塑料,另1款使用了聚氨酯等其它材料。而2013年(EuroCarBody 2013),菲亚达Alfa Romeo 4C和BMW i3车型车身使用了超过55%的塑料;铝合金材料也力图打破钢铁材料的垄断格局,大部分车型中都采用了数量不等的铝合金,最大比例达95%;有2款车型使用其它材料,如聚氨酯等。
表1:欧洲车身会议(2012-2013)汽车车身用材料结构分析
年度
|
车型
|
钢铁(%)
|
铝合金(%)
|
塑料(%)
|
镁合金(%)
|
其它(%)
|
合计(%)
|
2012年
|
Skoda Rapid
|
100.00
|
|
|
|
|
100
|
Audi A3
|
96.80
|
3.20
|
|
|
|
100
|
|
Cadillac ATS
|
95.60
|
4.40
|
|
|
|
100
|
|
BMW 3 Series
|
95.00
|
|
|
|
5.00
|
100
|
|
Mercedes-Benz SL class
|
12.30
|
86.10
|
1.60
|
|
|
100
|
|
Honda CIVIC
|
96.70
|
3.30
|
|
|
|
100
|
|
Range Rover
|
5.00
|
95.00
|
|
|
|
100
|
|
Ford Fusion/Mondeo
|
100.00
|
|
|
|
|
100
|
|
2013年
|
Alfa Romeo 4C
|
8.00
|
36.00
|
55.00
|
|
1.00
|
100
|
BMW i3
|
7.29
|
19.20
|
59.46
|
|
14.05
|
100
|
|
Ford Transit Custom
|
100.00
|
|
|
|
|
100
|
|
Honda FIT
|
100.00
|
|
|
|
|
100
|
|
Infiniti Q50
|
96.90
|
3.10
|
|
|
|
100
|
|
Lexus IS
|
97.60
|
2.40
|
|
|
|
100
|
|
Mercedes-Benz S-Class
|
64.50
|
32.50
|
3.00
|
|
|
100
|
|
Opel Cascada
|
96.00
|
4.00
|
|
|
|
100
|
|
Range Rover Sport
|
5.00
|
95.00
|
|
|
|
100
|
|
Renault Captur
|
96.60
|
1.70
|
1.70
|
|
|
100
|
从车身选材分析,由于冶金技术和加工工艺的提高和成熟,铝合金己成为汽车车身的重要材料,用于制造车身的发动机罩、行李箱盖、保险杠、车身内外板件、散热器等。从表1中可见,全新一代路虎揽胜运动版甚至采用了全铝承载式车身,较之前一代采用钢制车身结构重量降低了39%。而镁合金由于价格、高温抗蠕变及耐腐蚀性能等问题,在车身上还未大量应用。
2013年车型中,BMW i3为新能源(电动)汽车,为平衡电池组的重量,选择了塑料作为车身的主要材料,塑料用量占到59.6%,车身重量减少至223Kg;而FIAT的Alfa Romeo 4C则是一款全新设计的跑车,为了保证优异的提速和运动性能,釆用了55%的碳纤维增强塑料和硬质塑料,白车身重量仅213Kg。
2、车身用汽车钢板的发展趋势
作为最早用于汽车制造且仍然是汽车生产的主要材料,钢铁在不断改进以适应汽车各种设计变化的挑战。高强度汽车钢板的开发成功,很好地解决了轻量化与安全、成本之间的矛盾。与其它轻金属和复合材料相比,高强度汽车板具有良好的加工、回收性能和优异的性价比,仍是一种理想的轻量化材料。
欧洲车身会议发布各车型用汽车钢板的使用情况如表2所示。在汽车钢板为主导材料的车型中,使用的汽车板主要分为软钢(Mild Steel)、高强钢(HSS:HSIF、BH和HSLA)、先进高强钢(AHSS:DP、TRIP)、超高强钢(UHSS:CP、MS)、热成形用钢(PHS)和不锈钢。
2012-2013年欧洲车身会议车型,软钢汽车板主要用于车门内外板、顶棚、发动机罩等拉延要求高、不承担结构的零部件,仍是大部分车型中用量较大的汽车板之一,这与其良好的深冲性能和低成本优势分不开表2中13款以汽车钢板为主导材料的车型中,软钢比例为14.0%-59.2%,平均占比为39.2%(2012年为35.6%;2013年为42.2%,若不计Ford Transit Custom客货两用车则为39.4%)。而高强钢(髙强IF钢、低合金高强钢HSLA等)的比例为26.3%-52.1%,平均占比为35.5%(2012年为40.2%;2013年为32.6%)。先进高强钢(以DP为主)主要用于车体的结构框架中,形状复杂,需兼顾强度和成形性能,其比例最高(Ford fusion/Mondeo)达到23.9%,平均11.2%(2012年为10.5%;2013年为11.8%)。超高强度钢(CP、MS)主要用于汽车的结构梁类等要求有极高强度的部件,这类零件具有吸收能量的作用,还需与其它零件进行搭接,形状比较复杂,成形较难,从表2的数据看,其最高比例达到9.8%(Cadillac ATS),Mercedes-Benz S-Class达7.50%,平均为4.4%(2012年4.0%;2013年4.8%)。
表2:欧洲车身会议汽车车身钢铁材料分布情况
年度
|
车型
|
车身重量(kg)
|
钢材(%)
|
软钢(%)
|
高强钢(%)
|
先进高强钢(%)
|
不锈钢(%)
|
超高强钢(%)
|
热成形(%)
|
2012年
|
Skoda Rapid
|
329.0
|
100.00
|
42.88
|
46.95
|
1.63
|
0.00
|
0.00
|
8.54
|
Audi A3
|
309.5
|
96.80
|
35.20
|
26.30
|
13.60
|
0.00
|
0.00
|
21.70
|
|
Cadillac ATS
|
372.9
|
95.60
|
31.60
|
38.10
|
10.30
|
0.00
|
9.80
|
5.80
|
|
BMW 3 Series
|
402.0
|
95.00
|
25.00
|
54.00
|
9.00
|
0.00
|
4.00
|
3.00
|
|
Mercedes-Benz SL class
|
326.0
|
12.30
|
5.40
|
5.50
|
0.00
|
0.00
|
0.90
|
0.50
|
|
Honda CIVIC
|
360.9
|
96.70
|
45.70
|
39.90
|
4.70
|
0.00
|
1.40
|
5.00
|
|
The All-New Range Rover
|
379.0
|
5.00
|
0.00
|
4.00
|
0.00
|
0.00
|
0.00
|
1.00
|
|
Ford Fusion/Mondeo
|
428.4
|
100.00
|
33.40
|
35.70
|
23.90
|
0.00
|
3.60
|
3.40
|
|
2013年
|
Alfa Romeo 4C Coupe
|
213.0
|
8.00
|
2.00
|
00.00
|
4.00
|
2.00
|
0.00
|
0.00
|
BMW i3
|
223.0
|
7.29
|
7.29
|
0.00
|
0.00
|
0.00
|
0.00
|
0.00
|
|
Ford Transit Custom
|
635.4
|
100.00
|
59.23
|
26.84
|
5.74
|
0.00
|
0.00
|
8.19
|
|
Honda FIT
|
301.2
|
100.00
|
54.40
|
26.50
|
11.00
|
0.00
|
6.90
|
1.20
|
|
Infiniti Q50
|
381.5
|
96.90
|
44.70
|
21.30
|
22.80
|
0.00
|
5.90
|
2.20
|
|
Lexus IS
|
394.0
|
97.60
|
49.40
|
28.20
|
15.40
|
0.00
|
0.60
|
4.00
|
|
Mercedes-Benz S-Class
|
435.0
|
64.50
|
14.00
|
24.50
|
10.50
|
0.00
|
7.50
|
8.00
|
|
Opel Cascada
|
444.0
|
96.00
|
31.90
|
52.10
|
10.40
|
0.00
|
0.00
|
1.60
|
|
Range Rover Sport
|
353.0
|
5.00
|
0.00
|
4.00
|
0.00
|
0.00
|
0.00
|
1.00
|
|
Renault Captur
|
353.0
|
96.60
|
41.70
|
41.60
|
6.50
|
0.00
|
3.10
|
3.70
|
总体来讲,高强度汽车板应用比例平均达到55.9%,最高达到70%(BMW 3 Series)。目前,国内汽车车身材料中高强度汽车板使用比例平均水平约40%(见图1),与欧洲和北美的水平比还有差距。
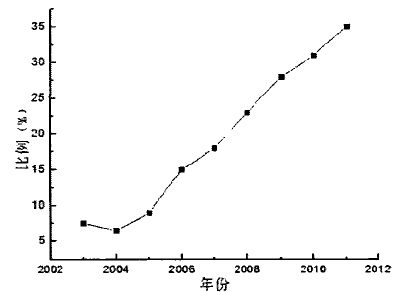
图1:国内高强度汽车钢板使用比例逐年增加
此外,从材料型深加工的角度看,欧洲和北美市场汽车板材料中冷轧退火汽车板约占85%,涂镀汽车板则达70%,汽车外板材料为19%。(如图2所示)
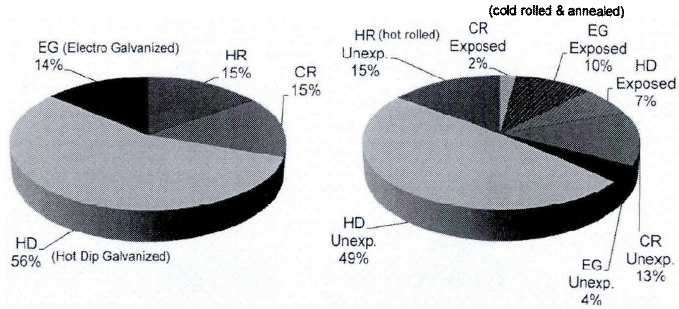
图2:欧洲和北美市场汽车板材料结构
3、汽车板深加工技术
在有色合金及塑料材料竞争的推动下,基于钢铁材料的汽车轻量化需求拉动了汽车板深加工技术及多维服务的迅速发展,促进了服务型深加工和产业型深加工的发展壮大。激光拼焊、液压成形、热成形和滚压成形等技术是汽车板深加工技术的主要形式,它们支撑了汽车轻量化的发展,同时又在轻量化的实践中升级进化。
热成形零部件在汽车车身上的大量使用,得益于热成形技术的快速发展。在基于均一材质与厚度尺寸的传统热成形技术的基础上,voestalpine和Benteler(图3)等开发了结合激光拼焊板的热成形技术、梯度回火热成形技术和局部热处理热成形技术等。在新技术支持下的热成形零部件,具有更好的强度、抗腐蚀性能、梯度功能、抗冲击能力、尺寸精度、加工连接性和经济性。
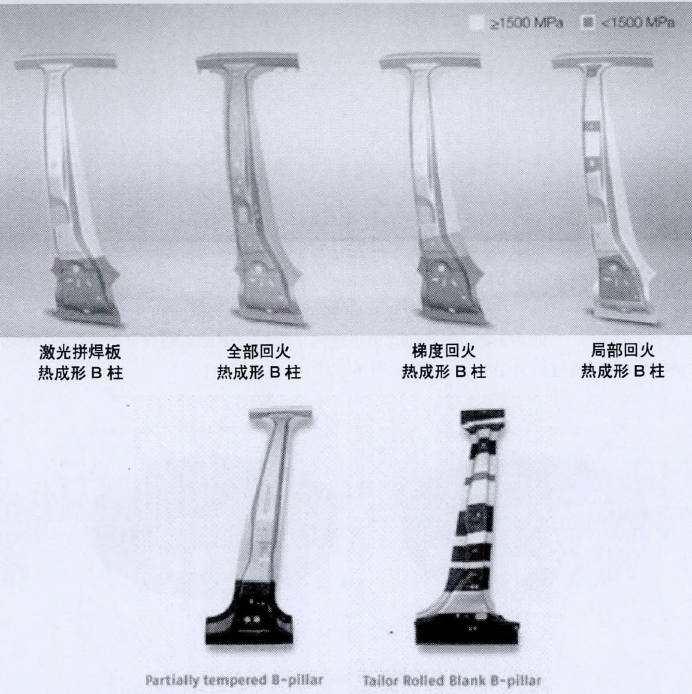
图3:本特勒(Benteler)基于部分回火及激光拼焊卷技术的B柱
热成形技术的发展和应用,使得白车身的减重效果得到更大发挥。当采用强度更高的热成形零部件时,不仅可减少零部件厚度,而且零部件个数也可以减少。近年来,白车身中使用的热成形零件覆盖面持续增大,使用比例不断攀高。从表2中可知,2012-2013年欧洲车身会议共有16款车型用到了热成形零部件,平均占车身重量的6%,而新Audi A3最大比例达到21.7%。来自通用汽车的资料也显示了同样的趋势,目前其新车型热成形零部件比例约为12%,到2018年预计会上升到25%。
激光拼焊技术从发明应用至今己30年,技术日臻成熟,产业不断壮大,近年来又开发出激光拼焊卷板技术,大幅度地提高了生产效率。滚压成形技术(Rollforming)近年来广泛应用于轻量化汽车零部件的制造,图4展示了奥钢联生产的长条形滚压成形零件。在此基础上,Mubea公司开发了变厚度板卷制造技术,并与滚压成形工艺结合,创新性地发明了TRB技术,开拓了汽车板深加工技术的新领域。
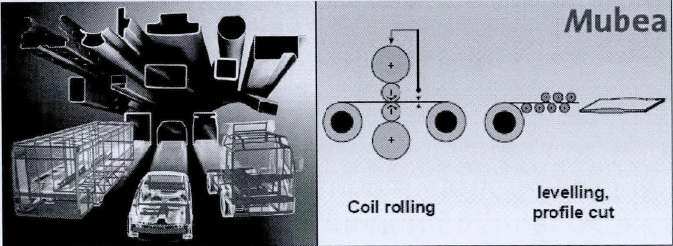
图4:奥钢联(voestalpine)的滚压成形技术;图5:Mubea的TRB滚压成形技术
汽车板深加工技术的发展还在于将激光拼焊、液压成形、热成形和滚压成形等技术优化组合,大大地拓展了深加工技术模式,提供了更多轻量化加工的可能性。图6是世界钢铁协会对材料深加工技术的组合优化分析。
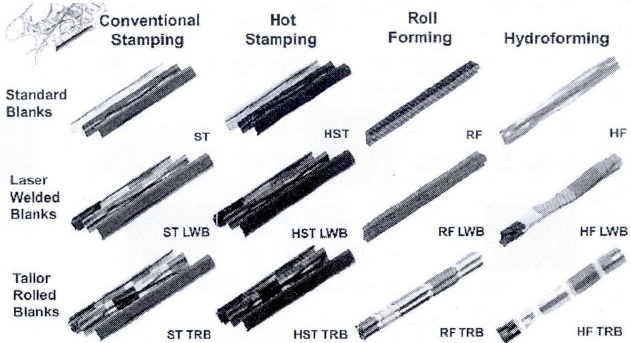
图6:材料深加工技术的组合优化
正是由于上述先进深加工技术的创新发展,基于高强度汽车板的结构优化的轻量化车身才更具竞争力。图7(通用汽车Cadillac)和图8(新Audi A3)是高强度汽车板材料在典型轻量化白车身上的应用。

图7:通用Cadillac白车身用汽车板材料结构(高强度汽车板用量达80%)
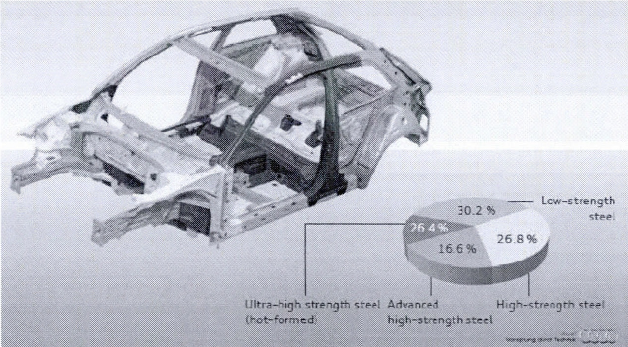
图8:新Audi A3白车身用汽车板材料结构(2012年)
(白车身重量246.5kg,大量使用的热成形零部件占21.7%)
4、结语
1)近年来汽车车身中汽车钢板仍然是主体。但随着汽车车身轻量化需求的日益提高及轻量化技术的快速发展,铝合金等有色金属材料、工程塑料和碳纤维等非金属材料逐步提升了其综合竞争力。
2)为满足汽车轻量化的发展,汽车板在材料型深加工方面必须向高强度、高成形性和涂镀耐腐方向发展,才能在材料竞争中继续站稳主导地位。
3)在汽车钢板材料组合中,IF钢、高强IF钢汽车板总体上将保持一个稳定的份额;高强度DP双相钢市场成长空间较大,强度将向1200MPa级发展;TRIP钢的发展因回弹问题、加工困难和高合金成本等原因将受到抑制;热成形汽车用钢及零部件将进入快速发展阶段。
4)激光拼焊(TWB)、热成形(HPF)、液压成形(Hydroforming)和滚压成形(TRB)等汽车板先进深加工技术,竞相发展升级,但并非相互取代,形成轻量化技术组合,是汽车轻量化发展的必要支撑,也推动了钢铁材料的发展。
5)以先进深加工技术发展为基础,汽车板零部件深加工产业将获得持久而稳步发展。